点击【 大 中 小 】,可以选择字体的大小,以便你阅读.
1 引言
工程公司主要生产液氯钢瓶、液氨贮罐及氮气包等各种三类容器。由于该类容器属于剧毒、高压类容器,其工作压力一般在(2.0~16.0)MPa,因此对热处理的要求也特别高。
公司原有热处理炉的炉膛长12m、宽3.6m、高4m,热处理炉共有14个加热点,即14个燃气喷嘴,左右两侧的下方各均匀地排列7个。另有4个温度检测点。在热处理过程中,工人要密切注视着热处理炉中温度的变化,根据热处理工艺要求及当前温度值的大小,经常调节进气量的大小以达到控制炉温高低的目的。由于热处理炉的容积较大,故热处理炉内各部分的温差也较大。在一次设备的热处理过程中,工人往往要进行数十次进气量的调整。这种控制方法不仅增大了工人的劳动强度,更重要的是热处理炉进气量调节的幅度是工人凭经验来进行控制的,加上温度变化的滞后性较大,常常会因为操作不当而引起炉内各处温差较大或温升速率偏离热处理工艺要求过多(一般要求温升速率为100℃/h),使得被处理的设备可能会由于“严重网状”而产生裂纹;有时也可能会因为加热不足或过热等现象,使得被处理的设备表现出硬度不足、球化不完全或晶粒粗大、碳化物粗厚等疵病。
热处理质量一般需要通过专门的仪器才能得到鉴定,而要对出厂的每一个设备都做这样的鉴定是有一定困难的。所以热处理质量的好坏关系到设备使用的安全性能。为提高热处理过程中的自动化程度,改善热处理效果,保证产品质量,提出了对原有热处理炉进行改造,设计一个新型的热处理炉。
2 热处理炉控制系统的设计
2.1 系统结构框图
热处理炉控制系统结构如图1所示。为实现对热处理炉进气量的均匀控制,将原来1个点上只有1个喷嘴改成1个点上有3个喷嘴,这样热处理炉由原来的14个喷嘴增加至42个喷嘴。但总的进气量基本保持不变。热处理炉控制系统在工作中视炉内温度的高低来决定打开几个喷嘴。另外,为准确反映炉内温度,温度检测点也由原来的左右各2个变成左右各4个,再加顶部4个,总共有12个温度检测点。系统选用日本三菱公司的FX2N-128MR作为数据采集、逻辑控制及实现PID调节的主控单元;选用上海嘉松机器有限公司生产的ZCZG高温电磁阀作为进气控制的执行元件。
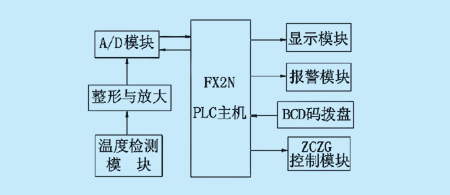
图1 热处理炉控制系统结构图
2.2 系统工作原理
系统人机对话功能模块由BCD码拨盘、显示模块和声光报警等部分组成。BCD码拨盘用来完成给定温度的设定和温度检测点的选择等功能;通过BCD码拨盘的切换可显示炉内任一个温度检测点的温度;系统的控制信号是根据传感器所检测到的温度与给定温度进行PID运算后直接驱动可控硅对ZCZG高温电磁阀进行控制;电磁阀通电后,阀中的连杆被提升,之后转轴开始转动并作用于导阀从而打开主阀,断电后,在衔铁自重及返回弹簧作用下关上导阀,靠压差关闭主阀;当系统检测到温升速率大于给定温升速率或恒温时温度偏离允许的范围,系统都会为发出声光报警。
2.3 PID调节算法及系统主要参数设定
在由数字PID调节算法来实现控制的系统中,过程控制对象需要的是控制对象的绝对值,而不是其增量。目前常用的PID调节算法有位置式算法和增量式算法两种。位置式算法每次输出均与整个过去的状态有关,计算式中要用到过去误差的累计值,因此容易产生较大的积累误差。而增量式PID算法只需要计算其增量,计算误差或精度不足对控制量的影响相对较小。故系统数据运算时采用增量式算法,而输出控制采用位置式算法。其运算式为:
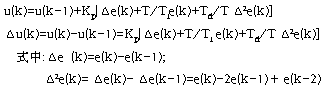
PID调节算法中参数的选择是关系到PID调节性能好坏的关键所在。若简单地用试凑法来整定PID的调节参数,需要进行多次的模拟或现场试验才能得到所需参数。若先将调节器选为纯比例调节器,并使之形成闭环,再根据经验数据,使系统对阶跃输入响应达到临界振荡状态,这时的比例系数记为Kr,临界振荡的周期记为Tr。根据齐格勒-尼柯尔斯(Ziegle-Nichols)提供的经验公式,可求得不同类型调节器的参数。考虑到控制对象的特点,经过试验,最后确定比例常数Kp=4.5、积分常数Ti=8.0、微分常数Td=2.8。