点击【
大 中
小 】,可以选择字体的大小,以便你阅读.
1 引言
PLC作为一种成熟稳定可靠的控制器,目前已经在工业控制中得到了越来越广泛的应用。PLC系统的设计直接影响着工业控制系统的安全可靠运行。一个完善的PLC系统除了能够正常运行,满足工业控制的要求,还必须能在系统出现故障时及时进行故障诊断和故障处理。故障自诊断功能是工业控制系统的智能化的一个重要标志,对于工业控制具有较高的意义和实用价值。
故障诊断一般有两种途径:故障树方法和专家系统方法。故障树方法利用系统的故障逻辑结构进行逻辑推理,由错误的输出找到可能的输入错误。这种方法比较适用于系统结构相对简单,各部分耦合少的情况。专家系统方法通过建立系统故障的知识库与推理机,计算机借助现场的数据利用知识库和推理机进行深入的逻辑推理,找出故障原因。这种方法适用于系统结构复杂,各部分耦合强的大型工业系统。
本文根据故障树推理与专家经验规则推理相结合的方法,以某火电厂输煤控制系统的设计为例,介绍了一种利用PLC和上位计算机进行故障诊断的PLC系统设计。
2 系统设计
故障诊断系统建立在基于PLC和上位计算机组成的控制系统上。PLC在故障诊断系统中的功能主要是完成输煤系统设备故障信号检测、预处理,转化存储并传输给上位计算机。上位计算机由于具有强大的科学计算功能,利用专家知识和专家库,完成从故障特征到故障原因的识别工作。并通过人机界面,给出故障定位,报告和解释故障诊断结果,并为操作员给出相应的排除故障的建议。
3 PLC程序设计
在进行故障诊断设计时,首先必须对整个系统可能会发生的故障进行分析,得到系统的故障层次结构,利用这种层次结构进行故障诊断部分的设计。以火电厂输煤控制系统的故障结构为例。为了描述简单,这里作了一定的简化。图1为系统的故障层次结构。
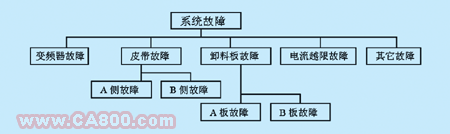
图1 系统故障层次结构
系统故障结构的层次性为故障诊断提供了一个合理的层次模型。在进行系统的PLC梯形图程序设计时,应充分考虑到故障结构的层次,合理安排逻辑流程。在引入故障输入点时应注意:必须将系统所有可能引起故障的检测点引入PLC,以便系统能及时进行故障处理;应在系统允许的条件下尽可能多的将最底层的故障输入信息引入PLC的程序中,以便得到更多的故障检测信息为系统的故障自诊断提供服务。
(1) 故障点的记录
为了得到系统的故障情况实现系统的故障自诊断,PLC必须将所有故障检测点的状态反映给内部寄存器,图2是用来记录故障点的部分程序。
IR4.02是输入的IO节点,表示A侧皮带信号,当输煤系统使用A侧皮带正常运行时4.02的值为1,当4.02变为0时,说明A侧皮带信号出了故障,此时利用上升沿微分指令记录这次的信号跳变。这样这次事故就记录在IR31.00中。程序设计中将IR31作为记录底层故障信息的寄存器,由于内部寄存器IR有16位,所以能够记录16种不同的故障原因。如果有更多的故障需要记录,可以设置多个寄存器字。需要说明的是,有时引起故障的原因可能不止一个,往往一个故障会引起另一些故障的发生,因此还有关键的一点是程序要能记录最先发生的故障。这也需要通过PLC编程实现,程序只对最开始发生的故障敏感。
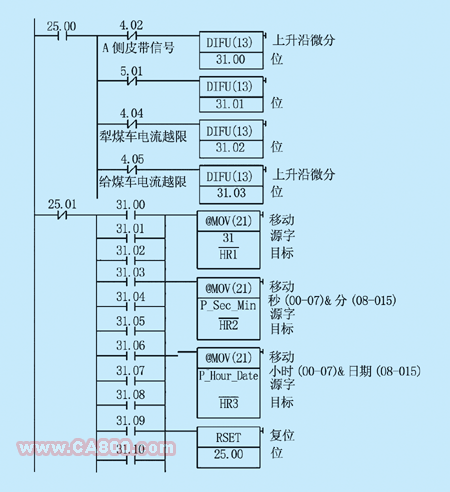
图2 记录故障的部分PLC程序
(2) 多次故障事件的记录
由于系统实际长时间的运行中,可能会出现多次故障,为了检修和维护方便,还需要PLC能够将多次故障事件记录下来。OMRON C200H型PLC的数据存储区(DM区)可以间接寻址,利用这一点,可以在DM区划出一定的区域,用来记录每次故障事件,包括故障类型和事件发生的时间(日期,小时,分钟,秒)。这一段DM区域可以循环记录,实际使用中记录了最后50次故障的情况,这些记录是系统运行的重要资料,方便了运行人员了解设备情况,对其进行检修和维护。