点击【 大 中 小 】,可以选择字体的大小,以便你阅读.
1 引言
组态软件通过I/O驱动程序从现场I/O设备获得实时数据,对数据进行必要的处理后,一方面以图形方式直观地显示在计算机屏幕上,另一方面按照组态要求和操作人员的指令将控制数据送给I/O设备,对执行机构实施控制或调整控制参数[1,2]。
目前,企业办公自动化已经基本普及,Windows操作平台以及微软的COM/DCOM/OLE 技术已成为应用软件之间通信的事实上的标准。在生产控制领域,DCS、SCADA、PLC等技术已经成熟,各种现场总线标准正在迅速推广。但是,管控一体化存在一个严重的制约因素,即现场设备与应用软件之间难以实现开放的、无缝隙的连接。
在生产现场,存在着大量控制器和现场数字设备,这些设备来自不同的制造商,遵从不同的通讯标准,只能组成各自的控制系统,与特定的应用软件通讯。虽然某些网络之间可通过协议转换实现互联,但并不具有普遍性。
传统的过程控制系统中,为使每一个应用程序与设备交换信息,必须为每个设备提供相应的驱动程序,在数据源与客户程序之间分别建立一对一的驱动连接,如图1所示。
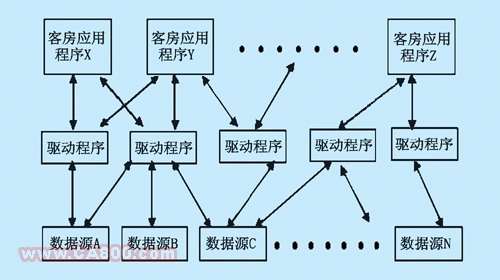
图1 传统的应用软件与数据源接口方式
由于设备多样性和驱动程序不兼容性,这种方式存在以下缺陷:
(1) 应用程序开发者必须花费大量精力开发各种设备的驱动接口,计算机硬件厂家要为不同的应用软件编写不同的驱动程序,这种程序可复用程度低,不符合软件工程的发展趋势,典型的高级语言软件开发过程约有25~30%的时间用于编写这类接口,使开发时间和费用大大增加;
(2) 设备不具有互操作性,使用中硬件的升级、变更和增加都可能造成驱动程序的变化,从而在维护过程中引起二次投资;
(3) 由于每一驱动软件有各自的驱动程序,当多个应用软件读取同一数据源时,经常生冲突;
(4) 设备厂商虽然可能提供驱动程序,但与用户开发应用软件往往不一致,限制了用户对软件和设备的自由选择。
可见,在现场设备与应用软件之间提供标准的接口,实现开放的、无缝隙的连接,是顺利推进企业管控一体化的关键。为此,在微软的倡导下,世界范围内处于主导地位的硬件和软件开发商组成了OPC基金会组织(OPC Fondation),制定硬件和应用软件之间的接口标准-OPC规范。文章对有关问题作如下简要讨论。
2 OPC产生的背景
OPC(OLE for process control)即用于过程控制领域的对象链接和嵌入技术,这一概念是由Fisher Rosemount公司1995年首次提出的,它借用了微软的OLE(Object Linking and Embedding)和COM(Component Object Model)/DCOM( Distributed Component Object Model ) 技术,并应用于过程控制中。它为过程控制和工业自动化领域提供了一套标准的接口、属性和方法,是实现控制系统现场设备与过程监控级进行信息互连,实现控制系统开放性的关键技术[4,5]。
提出OPC技术最初是为了解决应用软件与各种设备驱动程序的通信问题,简化系统的I/O驱动开发方式。没有采用OPC技术以前,对一个有M种应用程序、N种设备的系统,共需开发M×N个驱动程序,而OPC采用客户/服务器体系,为服务器与客户程序的链接提供统一、标准的接口规范。采用了OPC技术以后,只需要开发M+N个与OPC的接口,如图2所示。

图2 采用OPC方式的应用软件与数据源接口方式
正是OPC的这种数据访问特点使得使用OPC技术有很大的技术优势和经济优势。它的优点概括起来大致有以下3个方面:开放性(Openness)、高生产率(Productivity)、和“即插即用”的可连接性(Connectivity),因此可以说