来源:controldesign
WHEN A ROBOT slammed into a slide-mounted weld gun at Citation Global Manufacturing a few years ago, the now-defunct company’s mechanical engineer stared at the two devices for a few seconds, and said, “Well, that didn’t happen on paper.”The weld gun hadn’t completely returned to its home position before the robot tried to occupy the workspace, and so the robot didn’t have enough clearance to avoid a collision. Citation’s staff fixed their machine on the plant floor, but the real-world accident and resulting downtime could have been avoided if the weld gun and robot had been running earlier in a 3-D simulation.
从仿真(模拟)到基于web的诊断,系统设计工具正在将CAD和CAE制图推向现实世界,在个别机器制造以前,这些工具有时还可以预先模拟其操作。
当几年以前Citation Global Manufacturing公司机器人向滑块焊枪猛烈撞击时,这家现在已经倒闭的公司的机械工程师盯着两个设备看了几秒并且说,“喔,那件事在理论上是不会发生的。”在机器人到达工作区域之前,焊枪没有完全回到原位,所以机器人没有足够的空间去避免撞击。Citation公司的工作人员只好修理现场的机器,但是如果对焊枪和机器人的操作进行预先的3-D模拟,那么实际发生的事故及其导致的停工时间就可以避免。
“一个优秀的仿真和验证软件可以提前去掉这样的问题,并且可以确定逻辑转换是否正确或者是否需要延长周期。” 当时Global公司的控制工程经理Mark Taylor说,“然而,如果包括开关、接线和周期等所有这些参数在仿真过程中都不精确,那么用户将出现问题并且导致停工。当然,用户要知道,他们可以用仿真来设计过程以外的问题,利用动态数据流可以使仿真更接近实时。”
那么,什么时候图像才能转变为现实呢?仿真转变为实际操作的关键点是什么?理论上,和从行为判断人一样的道理,当图像显示的和真实事物发生相吻合的时候,它可以被定义为现实。当感觉图像所显示的内容能对其环境起作用的时候,便可以断定它属于现实世界的范围了。
当然,图像已经足够真实。但是石洞壁画毕竟不能捕获动物,一幅蓝图毕竟不能代表头上的屋顶,最优秀的、最详细的、最高分辨率的CAD/CAM制图也不能独立地表达每个机器独有特点和环境缺点,正如仿真不能操作机器的整个应用过程一样。难道它能吗?
仿真正在不断地向现实世界近一步靠拢,一些以软件为基础的设计工具已经发展到足够复杂,在制造所需要的机器前,不仅可以模仿很复杂的设备,而且还可以融合特殊的测试、PLC和其它来自独特应用软件的数据。提前配置和提前测试和起来就是“试运行”。
事实上,CAD很久以前就有添加特定应用软件数据的功能了,但其设计水平需要增加和快速抑制,因为要对像重力和摩擦力这样的自然力进行仿真。然而,无论如何仿真都与现实有关联,仿真越接近原型的工作状态,越多的缺陷就会提前解决,实际制造期间或制造后的修正就会越少。在保持足够的计算能力达到有效的仿真的情况下,通常使用的办法是简化设计。
例如:当设计用来印制电路板的新型General Surface Mount (GSM1)贴片设备时,纽约Binghamton 市Universal Instruments公司必须改进系统轴头和Z轴的装配,并且设计可以支持轴头包括10毫秒建立时间在内的加速和减速特性的机械元件。 Universal公司的运动控制工程师Jim York说,他的公司用仿真软件将屏幕上的预定功能块和GSM1伺服驱动器中特有的模型属性连在一起,这些属性包括位置,速度、电流控制以及影响索力的包括加速和减速特性、负载量、刚度特性和摩擦力等所有参数(见图1)。
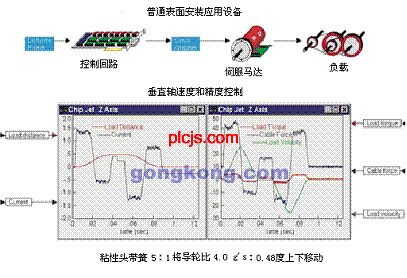
图1 虚拟目标接线
Universal Instruments公司在制造GSM1贴片设备前采用仿真软件模拟其实际电流、负载位移、负载转矩和电缆轮廓
York说,“通过弹出的对话框在适当的模块中直接输入元件操作参数,仿真时,我们可以通过图像和实时曲线观察电缆张力的动态变化。输入已知的加速度、减速度和负载量时,我们可以立刻观察到其对张力的影响,这样就能调整刚度特性从而保持张力一直为正。”
“与组装电路试验板和进行物理测试相比,应用仿真可以让我们以更快的速度设计GSM1。同样,GSM1仿真精度高,能够让我们分析在电路试验板中很难观察到的信号。因为可以看到整个机械负载的动态图像,所以我们就可以设计元件使其适合垂直轴上加速和减速特性,确保当负载上下移动时对它的严格控制。通过仿真验证设计方案,我们就可以在制造原型之前确定恰当的元件,这样就显著地缩短了设计周期。”
仿真是基本需要
在机床控制方面,仿真普遍用在校验零件程序、程序执行或机器计量应用中数据采集有效性。仿真人员同样在将新型电子和外围设备系统与实际的工作母机结合以前,要测试它们的结合状态。
例如,Wärtsilä公司以前使用手工C语言代码为共轨电子式燃料注入燃油式柴油机单元开发嵌入式控制系统,这样做虽然对船舶推进和发电装置应用的改进起到促进作用,但是这种比较老的程序成为了工程组人员制定明确规范和沟通的障碍。
“基于C语言的开发也是极其困难而且需要太多的引擎测试,”Wärtsilä公司自动化专家Ari Saikkonen说,“针对详细的软件模型,我们需要集成的动态仿真用来进行应用中的测试,要有足够的精确性以保证在实际引擎上第一次运行的时候不会出现问题。”
Wärtsilä 公司决定使用Math Works公司的Simulink软件来设计和模拟其系统模型,用Real-Time Workshop嵌入式编码器软件来从模型中自动生成产品代码。公司的工程师凭借这些工具利用分级结构图和状态机来描述复杂的函数和算法。他们进一步应用 Simulink模拟这样的控制算法功能,比如PID控制、燃料限制和前馈控制。Wärtsilä公司还创建了元件库来帮助工作人员组装和处理大型应用,这也意味着重复性工作更容易完成,因为设计更加明确而且与提供的工具相匹配。
“对于RAM、ROM和执行速度来说,自动生成的代码比手工代码要强得多,”Saikkonen说,“我们预计已经将代码缩减到原来的百分之三十,将CPU执行时间减少了百分之二十。高度的提取、改进的结构和自动产品代码使生产力提高了两到三倍。”
由于用仿真软件模拟机床控制系统非常复杂,先前用户曾制造不能与实际机床相连接的独立控制系统模型,这样他们就可以测试控制系统,风险和难度也降低了很多。这些模型在后来尤其是在过去的两三年里越来越以软件为基础了。实际上,仿真软件目前可以模拟数控机床系统的精确控制。
“我们没有理由被仿真吓倒。”美国密歇根州Farmington Hill市系统集成商VI Engineerng公司首席营运官Dean Streck说,“这曾经是和复杂的,但是现在用起要比五年以前容易得多且成本更低。”
例如,GE Fanuc公司为其30i控制系统设计的仿真软件可以复现实际机床控制系统上所有的功能。其模型可以检查控制系统控制产品生产方式的部件程序所有的编排,而且还可以检查作为机器界面的梯形图程序。这样模型就可以测试这两种程序,开发和测试机器的应用,也可以进行更好的培训。“对部件程序和机床内部发生的实际动作进行仿真对于培训有很大的帮助,因为你可以观察到机器内部运行状况,不需要实际的机器,就可以在PC机上进行操作。”GE Fanuc公司数控机床产品经理Gary Highley说,“这样用户就可以看到模拟夹盘中的工具,更换工具,监视模拟切割过程。这就意味着用户可以在不必安装价值十万美元的机床的情况下进行机床操作培训。”
可靠的数据=高质量的仿真
与所有的控制和自动化分支以及许多其它领域类似,真正有用和具体的仿真依赖于输入数据的质量。
“通过仿真,我们可以完全模拟任何系统的非线性特性以及现实存在,通过测试用户应用中的数据来调节模型。”Math Works公司市场经理Tony Lennon说,“然而,仿真也依赖于用户对其应用的了解程度和他们对设计和建模的投入程度。这种设计以模型为基础,通过采用可用来同时产生后续控制系统的可执行规则,用户就能够进行仿真了。Math Works公司的Simulink软件也允许用户使用可以在实时应用中运行的C语言代码。”
使用仿真的每个人都知道无用输入与无用输出。“问题是:如何得到良好的数据,怎样使其成为设计环境的副产品或者设计过程的核心?”ePlan Software &Services公司当前的副总裁兼总经理Taylor说,“许多人仍然在CAD中手工采集电子图像和图表,从数据库中将其加入CAD环境中,这样可能导致连续性问题。真正的数据库环境能够使数据操作和到仿真的数据传递更加容易,因此,代替现有的图像采集进行仿真,我们使用动态的精确的系统数据来为仿真工具生成图像,可以减少无用输入和无用输出。”
Taylor表示,低质量的数据是过去仿真没有更多发展动力的一个重要原因。“先前一把系统中的数据与实际不一致,这就导致数据设置对于有用的仿真来说没有足够的代表性,”Taylor说,“现在,用户正开始理解和转向基于数据的工程,代替了通常的CAD工程。”
仿真物理环境
为了对实际的机器应用有所帮助,在其制造和安装以前,仿真可以再现对设备起作用的物理力和其运行时所表现出来的力。“所有的仿真都要归结为数学,” Visual Solution公司的销售经理Jim Webb说,“仿真是从数学基本原理上建立起来的,这些原理可以重新归纳出比如弹力等的一些性质。通过确定精确的反映现实事物的模型,仿真与现实世界就结合起来了。例如,如果在调整一个模拟过程时,其值在10到12之间变化,那么你就可以知道在实际中调整时,其值也应当在10到12之间。这与校正仪器是类似的。一旦确信模型正确,你就可以将其放在一边,进行各种好的或者坏的假设分析,观察控制器的响应。”
美国密苏里州St. Louis 市的一家系统集成商Automation and Control Concepts 公司总裁St. Louis解释说,“仿真并非十全十美,所以我们必须注意被仿设备在现实中可能遇到的故障和响应。”
Schneider Electric新开的咨询部门Dextus公司的Dan Rackleft说,开发者以3-D几何学为起点,加入运动学特性使图像动起来,然后用软件工具来模拟质量、速度、压力、摩擦力、转矩、气压和所有现实世界中设备表现出来的其它必须的物理量。比如,Dextus 公司正在用ePlan 公司的仿真软件包帮助校验和控制机器部件的周期,避免应用中潜在的碰撞。理论上,随着软件的完善和计算能力的进一步增加,开发者计划模拟越来越复杂的设备、控制系统、机器、生产线以及全部的设备。
“人们必须意识到仿真不是卡通片,是可以信任的,和实际系统一样是可以用来使用的。” Delmia公司全球市场执行理事Robert Axtman说,“在制造和安装生产系统以前,你可以设计周转时间和物质流量,优化生产系统。目前有百分之八十到九十的系统在功能上提前检验合格,这就能帮助用户实现其起步生产目标并且节省了成本。”(见图2)
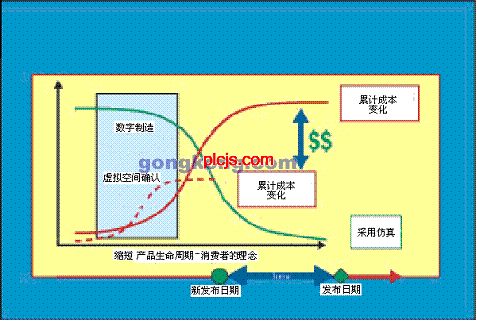
图2 实际成本节省情况
Delmia公司报告中指出,在虚拟世界中解决了设计错误问题,不但节省了机器改造的成本而且缩短了实际中投放市场的时间.
电气与机械工程师的合作
除了改进实际的机器,仿真工具正在给工程师和公司协作带来新的机遇——虽然很多人看起来并不情愿这样做。
“对运行的机器进行完全的虚拟测试是可能的,这样做也有充分的理由,但是这也需要一种文化的变迁。” Solidworks公司分析部门副主管Sujit Jain说,“例如,人们一般在部件生产阶段而不在装配阶段进行虚拟测试,设计师搜集这样的测试信息也已经有两三年了。然而,得到的数据先前仅对分析员有用,对其他人来说,甚至没有一个工作环节是轻松的。这意味着设计师不得不回到分析员的角色,然后他们才有希望跨越两个角色之间障碍而得到一些有用的数据。”
Jain补充说,日本Sumitomo类似于以分析员为基础的构造,对于已提交的资料,它有六到八周的周转时间,但其设计师用Solidworks公司的软件分析自己的基本机器功能数据,仅需要一周的时间。
“即使有了虚拟设计,你仍然可能需要在PLC控制中加入梯形图,或者在Solidworks设计中加入PLC算法,”Jain说,“在PLC层次上使用梯形图逻辑仍然有障碍,因为这个层次上出现的变化太快了。哪儿有可以将梯形逻辑连接到虚拟机的虚拟PLC系统呢?”
Solidworks 公司正与National Instruments(NI)公司在如何通过NI公司的LabView软件来进行Solidworks公司的驱动安装仿真方面展开合作。然而,Jain 表示,这些努力仍然是试验性的,得到任何有效的解决办法还得两三年时间。
尽管许多工程师可以利用仿真技术工具,然而他们很少与有潜在帮助能力的同事交流。“目前的问题是,在电气工程师和机械工程师彼此几乎不交流的情况下,如何让他们互相合作。”Jain说,“使用仿真进行合作听起来很棒,但是仍然有许多的障碍和文化问题需要克服。” 他补充说,如果开始交流,他们就可以通过使用Solidworks公司的Cosmos软件来查看应用分解图了。
“代表性地,只有当所有的机械、电气和机器人技术人员都行动起来并且物理设备在工厂安装好时,控制人员最后才进来调试一切,不过这已经太晚了。”Rackleft说,“这也就是我们想让虚拟综合和确认程序模拟所有这些物理设备和组装部件的原因,因此控制工程师可以在虚拟环境下调试和确认PLC、人机界面和其它机器组件。”事实上, Dextus公司正在用OPC服务器将一些比如按钮等等的3-D模型对象和实际的PLC和人际界面连在一起。,
这种新合作就是,轮流建立在其许多仿真工具提供的现实对应物的精确反映之上。“如果仿真周期是10秒,那么真实的设备周期也将是10秒。” Rackleft说,“比如,在系统中有20个机器人,这样的精确性让你必须考虑整个过程,说明每台设备完成工作所需时间,提前测试,在安装前检查错误并且在制造控制系统前进行确认。”
由于仿真一般寻求去掉规范上的不一致,所以Taylor说,欧洲仿真开发商和供应商正在追求“功能性工程”,通过实现某些功能而不是通过工程规范来建立仿真。“我们正在尝试达到一种无差别的程度,这种差别存在于建立3-D模型和建立数字模型所用到的工具之间,所以机器的启动与计算机现在还密不可分。”Autodesk公司的CAD/CAE产品总监Andrew Anagnost说,“这样就减少了设计的重复性并且减轻了用户的负担,因为推动设计几何学是机器的功能要求。”
这些目前和将来要实现的功效显示,仿真能够帮助保存也许是最重要的图像——考虑到了用户的账本底线而为其节省了成本。