点击【
大 中
小 】,可以选择字体的大小,以便你阅读.
1 引言
管道化溶出生产工艺的主体控制系统通过网络控制三个子系统,实现对整个溶出过程生产工艺参数的监视、安全连锁保护和生产管理;预脱硅、溶出、自蒸发、稀释、酸洗等工段电气设备的控制;自蒸发器及冷凝水器液位调节。隔膜泵控制子系统完成隔膜泵的同步控制、转速调节及连锁保护。熔盐炉控制子系统实现对盐泵、熔盐炉的连锁保护及熔盐炉燃烧温度控制。熔盐管路电加热子系统实现熔盐管路表面温度监测和电加热温度控制。
管道化溶出是在高温高压下溶出矿浆中的铝成分的生产工艺过程,具有能大大缩短铝矿石溶出时间,产量高,溶出指标高,节能降耗等优点,新建管道化已成为我公司氧化铝提产的急需,为保证新建管道化系统稳定可靠运行,根据管道化溶出的生产工艺要求及现有自控系统在实际生产使用中现状,对管道化自控系统进行了创新设计,自动控制系统分为:管道化主体系统、隔膜泵系统、熔盐炉系统、熔盐电加热系统等四大部分,系统以主体DCS为核心,下挂隔膜泵、熔盐炉、电加热三个相对独立的PLC子系统,通过控制网络相连,采用先进的计算机控制、仪表检测、电气技术,综合了集散系统、现场总线、可编程控制器及智能仪表,建成了管道化综合网络控制系统,自控系统结构如图1所示。
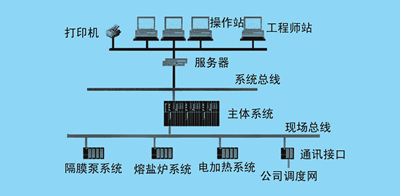
2 控制系统功能
2.1 主体控制系统
主体控制系统为管道化自控核心,它可以通过网络控制其他3个子系统,实现对整个溶出过程生产工艺参数的监视及安全连锁保护;预脱硅、溶出、自蒸发、稀释、酸洗等工段电气设备的控制;自蒸发器及冷凝水器液位调节。
自蒸发器及冷凝水器液位调节是主体控制系统的核心。自蒸发系统拥有多级自蒸发器用于完成反应后的矿浆的减温减压,延长矿浆反应时间,提高溶出率,其减温减压过程中所产生的蒸气用于对原矿浆进行预热,自蒸发系统液位的控制直接关系到溶出指标的好坏和系统的节能降耗。但由于自蒸发器之间依次连通,液位相互影响,因此,实现液位自动控制难度比较大,采用传统的控制方法难以达到满意的效果。而人工调节不仅劳动强度大,也不容易实现系统平衡。我们根据系统特点,利用过程控制系统的优势,采用模糊控制和PID控制,实现自蒸发器液位的自动控制,如图2所示。
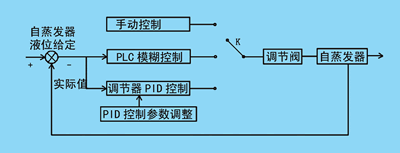
每一级自蒸发器对应一个单回路调节器,负责本级自蒸发液位控制,PLC作为监督管理控制部分,负责非正常情况下各级自蒸发器液位的控制以及正常情况下各调节器控制参数的动态调整。
控制设置手动、自动两种方式,当工艺、自动控制出现异常时,采用手动方式,通过计算机上单回路调节器面板直接控制阀门开关,调节液位。自动控制时,计算机自动判断当前自蒸发器液位状况,当系统刚开始运行或液位波动较大时,系统控制方式自动切换为模糊控制,根据各个自蒸发器当前液位和变化趋势,按照根据工艺要求和操作经验形成的模糊控制规则进行模糊推理,由计算机直接控制回路输出,对各自蒸发器阀门进行较大幅度的调整,当自蒸发器液位基本建立起来后,控制方式切换至PID控制,控制权交单回路调节器,在基本稳定的情况下,由调节器对自蒸发器液位进行调节,在此过程中,计算机随时监视各调节器的运行情况,根据内置的专家知识库,对调节器控制参数进行调整,及时调整系统的反应速度,控制精度,稳定整个自蒸发系统的液位平衡。使控制效果维持在最佳状态。
冷凝水系统与自蒸发系统控制原理类似。
2.2 隔膜泵控制子系统
隔膜泵控制子系统完成隔膜泵的同步控制、转速调节及连锁保护。
隔膜泵为管道化生产流程中的关键设备,通过其实现系统的升压。隔膜泵国产化后采用四台泵联动,变频调速实现300m3/h的进料量,为保证运行过程中出料管内压力平衡,必须保证四台泵同步。泵运行的相位差信号采用旋转编码器配合高速脉冲采集模块实现,同步控制采用基准泵同步方式,以基准泵运转角度为标准,调节其余泵,以实现同步。